|
|
|
Based on positive
previous
experience, I opted to use polystyrene
boards and a sheet of 10mm poplar plywood
as baseboard and trackbed. |
|
|
The types of
polystyrene available from DIY
stores most commonly used for
modelling purposes are XPS
(extruded polystyrene, Styrofoam)
and EPS (expanded polystyrene, Styropor).
XPS has a higher density
(2845 kg/m3) and
therefore higher stiffness in
comparison to EPS
(15-30 kg/m3),
whereas the latter is a lot
lighter in weight (effectively
made up of 98% air) and easier to
cut and sculpt (although a lot
messier than XPS). But since
rigidity and stability was the
prime requirement, the layout
base is made up of two sheets of
30mm XPS (cut
to the correct size using a
jigsaw with a fine tooth blade)
and then topped with a 10mm sheet
plywood top. |
|
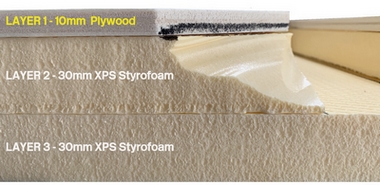 |
|
|
|
|
The bottom XPS
layer (#3) is the base, the second sheet
(layer #2) adds another 30mm height but
is also cut down in places to represent
below track level scenery, and the
plywood (layer #1) adds further stability
and provides a solid base for the track. |
|
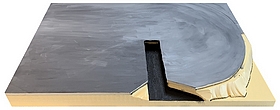 |
|
The
pre-planned sections for scenery
below track level were cut away
from the plywood sheet and the
mid-section (layer 2) of the XPS
(using a hot-wire cutter for the
latter). All three layers are
then locked together using
special polystyrene glue, and the
result is a lightweight yet
sturdy layout base.
Following
this, a liberal coat of acrylic
paint sealed the plywood
baseboard top - track ballasting
and scenicking involves no small
amount of a mix of water and glue
to fix it all in place, and
baseboards that haven't been
sealed this way may well start to
warp.
|
|
|
|
|
The layout baseboard is framed by four segments cut
from 10mm poplar plywood that have two functions. They
form the contours of the layout, with a backdrop that
slopes to the front, but also a solid and sturdy frame
which will allow a cover (think suitcase) to be attached
for transport and storage. |
|
|
|
|
|
|
|
|
|
Positive
previous experience in terms of stability, track
geometry options and visuals made Rokuhan my
choice of track for Gotham Central. Joining
individual pieces of track together is made easy
by the fact that the metal
rail joiners have an additional double-hook
plastic connector in the molded base of the
track, which also adds stability. Fixing
track pieces securely in place is a prerogative
for trouble-free running of trains. There are
several ways of doing that; some modellers glue
down the track, but Rokuhan provides a
"hidden alternative". |
|
|
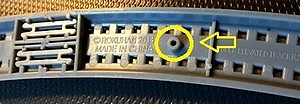 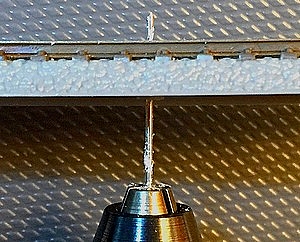
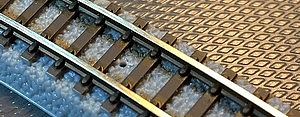
|
|
All but the shortest track pieces
come with guiding holes pre-moulded into the
ballast base, but unlike other track brands they
are invisible until drilled out from below - an
easy job using a Dremel with an ultra fine drill
and a low rpm setting. The
resulting small hole is just right to take
Märklin's Z Scale tracknails (#08999), my
prefered method of fixing down Z Scale track.
They are minute and visually unobtrusive, yet
provide a reliable and strong connection between
the plywood baseboard and the track. They can
simply be pushed home with a set of pliers and
therefore don't even require a hammer, avoiding
potential damage to the track.
An important aspect of
laying multiple parallel tracks is to maintain proper
spacing, and the wide availability of
laser-cut or 3D-printed items for Z Scale
provides various simple but effective tools to
ensure this.
|
|
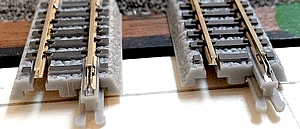 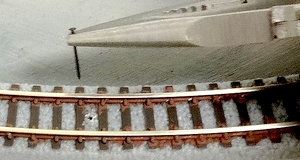
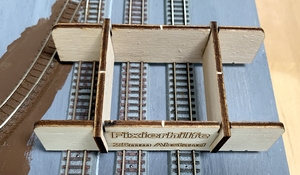
|
|
|
All of this ensures that
the track is properly joined, level, and fixed
securely to the baseboard. In terms of
trouble-free running, this is essentially all
that's needed. There are, however, a few
improvements that can be added to bring the
visuals closer to what railroad tracks look like
in the real world. In order to counteract the
lateral forces acting on a train running through
curved track (and thus reduce friction and
excessive wear of the wheels on the outer rail),
the track is laid with a cant, i.e. the outer
rail is raised above the inner rail, which
creates a banked turn. Given their low weight
(and resulting low lateral forces), models do not
require "super elevated track" in order
to run smoothly through a curve as long as the
train is run at reasonable speeds.
|
|
|
|
|
Almost all modellers will
agree that the clean and shiny appearance of
model track doesn't resemble what the real
railroads run on at all - rails
on the prototype always display a variation of
rust, dirt, grime and other residue from trains. As
with fixing down track, different methods and
preferences exist as to how weathering is applied
to the rails; for Gotham Central, track
weathering is done using track painting pens. |
|
|
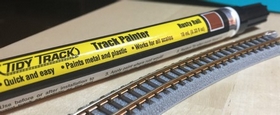 |
|
Woodland
Scenics offers three colour options
("rusty rail", "steel
rail", "weathered tie").
The rust colour pen usually needs two
applications unless the darker
"steel rail" is applied as a
base colour. The result looks good and is
done a lot quicker and tidier than by
paintbrush. |
|
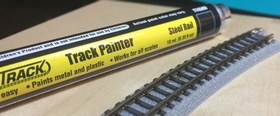 |
|
|
|
The
top of the rails then needs to be wiped
clean in order to ensure that electrical
conductivity is not reduced by the
weathering. All
of this is an attempt to artifically
recreate what happens quite naturally to
real track. If done properly, the rust
and grime adds an amazing level of
realism in comparison to
"untreated" track straight from
the blister pack. But even in Z Scale
there is more to recreating realistic
track: adding ballast. Using Rokuhan
track means that a ballast shoulder is
already molded in place, but some
additional ballasting goes a long way in
making it all look more realistic.
|
|
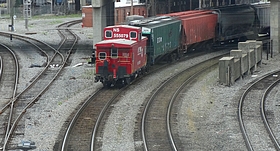 |
|
|
|
I use
Woodland Scenics gray ballast in
"fine" grade (B75).
It is just a bit lighter in
colour than the Rokuhan
trackbase, but for even more
convincing visuals a thin black
(and/or brown) wash can be
applied. I use a small food
storage box to provide a portable
"ballast hopper" from
which small quantities are spread
out along the edge of the moulded
ballast base of the Rokuhan
track, using a regular size
teaspoon - the back of which can
be used to tamp down the ballast
in a nice even slope to the
height of the sleepers.
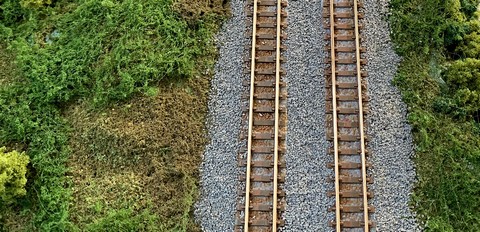
|
|
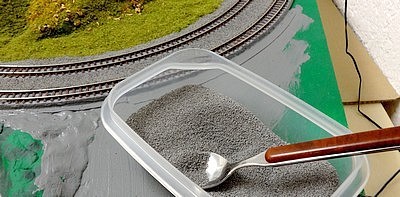 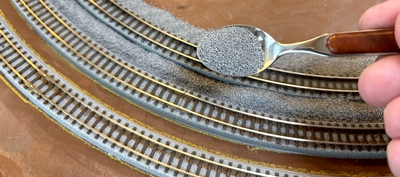
|
|
|
|
|
The ballast is then fixed
permanently in place. Traditionally this is done
using a 1:1 mix of white glue and water, but for
the sake of convenience and in order to avoid a
glossy finish I have found myself more and more
using Woodland
Scenics Scenic Cement™, which dries to a
clear matte finish. |
|
|
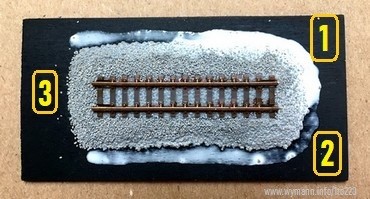 |
|
Without any
"pre-treatment" (such as spraying the
ballast with IPA), I simply apply the scenic
cement by taking advantage of its capillary
force. Because the scenic glue has a lower
surface tension than the ballast and scenic
material (thanks to the "wetting" agent
it contains), applying the mix close to the edge
of the ballast (area #1 in the picture) results
in the watered down glue being drawn in and
seeping into the dry ballast by itself - or
rather by its capillary force (2). Ultimately the
effect is similar to blotting paper or household
tissues sucking up liquids, and it leaves the
ballast almost completely undisturbed (3). The
illustration used here shows a piece of Z scale
track, but the principle obviously applies
regardless of scale. |
|
|
Letting the capillary
force do its magic does however result in a
slightly slower procedure. Starting at the edges
of the area to be treated, patience is required
to then let the scenic cement work its way
properly into the ballast and scenic material
(which might take a minute or two). Additional
scenic cement is then only applied to the areas
which have already soaked up the mix, saturating
them to the point where the mix then seeps into
the adjoining area of dry ballast and scatter
material. It is definitely a patience game, but
then ballasting shouldn't be rushed anyway. |
|
|
 |
|
When using
this method of ballasting, extreme caution is
required around any pointwork; since the bonding
agent is liquid it can easily seep into the point
mechanism and gum up moveable parts beyond
repair. |
|
|
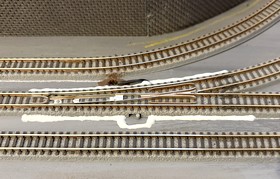 |
|
An
easy and efficient way to prevent this
from happening is to form a boundary
(akin to a "dam") with a bead
of white glue and then sprinkle on
ballast; once dried, any loose material
is diligently vacuumed off. To be on the
safe side, I only ballast the area
immediately around a point that way,
since white glue is viscous and therefore
a lot easier to control (especially
around the sliding knob that throws the
point). |
|
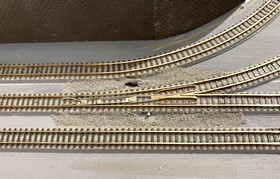 |
|
|
|
It is best to progress in small
steps when ballasting around points - definitely a
question of function over form. |
|
|
|
|
|
|
|
|
|
Even though the layout's scenery
is split up into distinct segments
("vignettes"), certain basic elements need to
be defined ahead of any detail secenery work. |
|
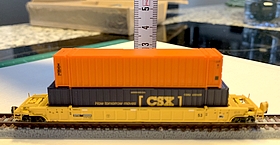 |
|
The
running lines pass under the top layer
scenery in several points on the layout -
which requires careful measuring of
rolling stock in order to ensure
sufficient clearances. Usually, double
stack container cars are the tallest
piece of rolling stock - but it turns out
that the extended pantograph of a GG1
reaches up significantly higher. |
|
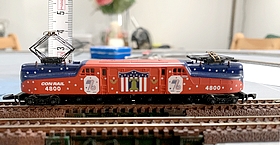 |
|
|
|
 |
|
Another
basic scenic element is the foundation
for the top layer (which carries no
track, only streets, bridges and houses).
Cut from lightweight yet stable
styrofoam, it provides the scenic
contours for the upper level scenery;
several different "vignettes"
will be built up on top of and around
this foundation.
|
|
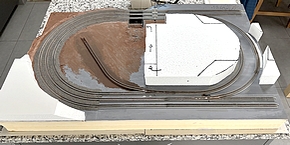 |
|
|
|
|
|
|
The first
scenic vignette was inspired by a slide in my
collection of a Conrail GP10
crossing a short girder bridge
over a secondary road. Loosley
interpreting the scene and
adapting it to the layout's urban
theme and track set-up, one
girder bridge became three and
the road turned into a single
railroad track.
The "three
bridges" vignette is the
only one that required advance
planning at an early stage of the
layout build. Because it is set
over two levels, the real estate
for the (non operational and
purely scenic) track running
below the bridges had to be
marked and cut during the
baseboard and trackbed assembly
stage.
|
|
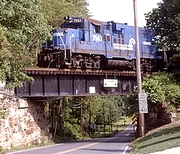 |
|
|
|
|
 |
|
The scene is
built up using regular Rokuhan track, Faller Z
scale styrofoam brick sheet (article #282942) cut
to shape, one Model Scenery World 3D printed
tunnel portal (all weathered with black wash),
three Rokuhan short green girder bridges (R086),
and a mix of Woodland Scenics brown ballast and
several scatter materials and bushes. work in
progress
|
|
|
|
|
|
|
|
|
|
|
|
Scenic
vignette #2 was inspired by a plethora of
vistas I encountered in books,
videos and photographs, depicting
railroads at work in front of a
backdrop of red brick industrial
buildings.
Putting something
similar onto the layout would not
only add a distinct scenic
vignette but also strengthen the
layout's overall urban theme. And
whilst town structure models
aren't as plentiful in Z as they
are in larger modelling scales,
German modelling accessory
specialist Kibri's injection
moulded kit of a turn of the 19th/20th century factory
building (article #36770) has been
available in Z Scale for decades.
|
|
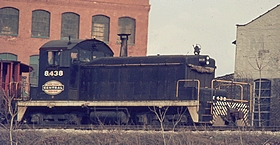 |
|
|
|
|
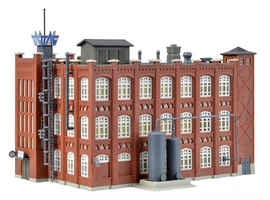 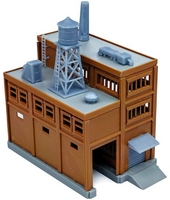 |
|
Given the
smallness of Z Scale it is a rather intricate
model, built up in classic fashion from injection
moulded parts supplied in different colours on
sprues. The factory scene is built up by
combining the Kibri factory with a very different
kind of Z scale factory kit - a somewhat cheaply
3-D printed mix of different colour parts that
come together to form a factory with loading
dock, made by Chinese company Outland Models
(article #BK711) and sold online.
There is a massive difference in price tags
(the Outland kit sells for around 10% of what you
pay for the Kibri kit), and this is obviously
reflected in their appearance.
|
|
|
A curiosity online purchase, the Outland Models kit
spent around ten years in a "for
later box" before finally finding a place and
purpose on Gotham Central. The kit is quite well
designed, with a dozen or so pieces that slot together to
form an interesting structure. The visuals, however, are
rather crude, with very obvious 3-D printing patterns (a
fact that Outland very openly points out on their
website) - clearly, this kit needs a substantial amount
of work, especially when placed right next to the
delicately moulded Kibri kit. Adding coats of spray paint
in an attempt to hide the most obvious printing patterns
and then break up the colour uniformity of the kit takes
it a notch or two up in appearance - also bearing in mind
that close-up photography is always somewhat cruel on Z
Scale models (but also shows you where some additional
clean-up work needs to be done). The
Kibri kit is, of course, an entirely different beast, and
a fairly complex (and at times fiddly) kit; I left off a
number of elements which seemed either too European or
just unnecessary for the purpose the building has on the
layout. Both kits were given liberal coatings of diluted
black wash as basic weathering.
The single spur leading to the
covered loading dock is connected to the inner circle of
track but really only intended as a scenic element. Since
Rokuhan's integrated ballast roadbed raises the track by
approximately 2mm off the baseboard, the surface around
the track (painted all-over in rust as a starter for
subsequent detailed weathering) required styrene sheets
in order to raise the buildings so that a boxcar (again
intended as an ultimately static scenic element) wouldn't
foul the loading dock frame. Raising the terrain like
this also makes it easier to model track that has
"sunken" into the ground.
work in progress
|
|
|
|
|
|
|
|
|
|
|
|
|
|
|
|

|
|
Any
commercial products mentioned here are purely bona fide
indications of what I have been using myself.
I have no connection to any manufacturing companies nor
do I profit from listing any products or brands.
|
|

|
|
page
created 18 February 2024
last updated 12 February 2025
|