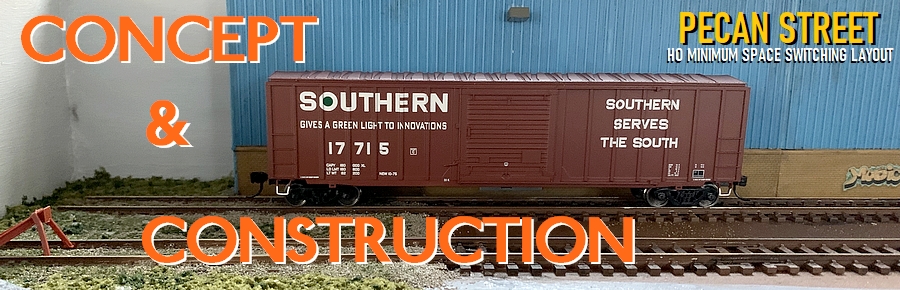 |
|
|
|
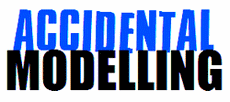 |
|
Pecan
Street is
very much the result of "trial and
error": every now and then, something went
slightly wrong or didn't work at all - or I
simply changed my mind and approached things
differently. It's what I call "accidental
modelling". Here's an account of how it all came
together in the end, step by step (which
is why there is also a certain amount of back and
forth).
|
|
|
Any commercial products mentioned
here are purely bona fide indications of what I have been
using myself.
I have no connection to any manufacturing companies nor
do I profit from listing any products or brands.
|
|
|
|
|
FIRST STEP:
PROOF OF CONCEPT
|
|
|
|
The prime question that needed to
be answered was what two tracks within a depth of
only 6 inches actually looked like in the real
world - something that no track planning software
is truly going to be able to show. A piece of
paper cut to the required width served as a
simple set-up for this "proof of
concept". It was always clear that it was
going to be tight, but the one thing I didn't
want was for it to feel overly cramped (which is
why a boxcar was set up on one of the tracks).
|
|
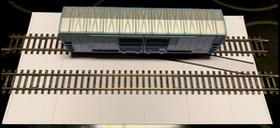 |
|
|
This is one of those "instant moments":
either it clicks, or it doesn't. In this case, I was
happy to move on and actually start building the layout. |
|
|
|
|
|

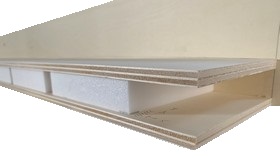
|
|
For the two
baseboard segments I returned to the construction
method used on Little Bazeley Mk2 which provided a solid yet
lightweight layout framework. Using a sheet of
10mm poplar plywood as the base, pieces of 20mm
styrofoam insulation are glued to that board,
which in turn is covered by another sheet of 10mm
ply in "sandwich style". Once
the side- and backdrop are added, this results in
a very sturdy yet lightweight layout frame and
basebaord (which also results in comparatively
silent running of trains).
There
is, however, one obvious problem with this
approach - there is no real cavity underneath the
trackbed-baseboard. In order to be able to run
cables underneath the baseboard top, the
styrofoam blocks are set back slightly, providing
some space at the front.
|
|
|
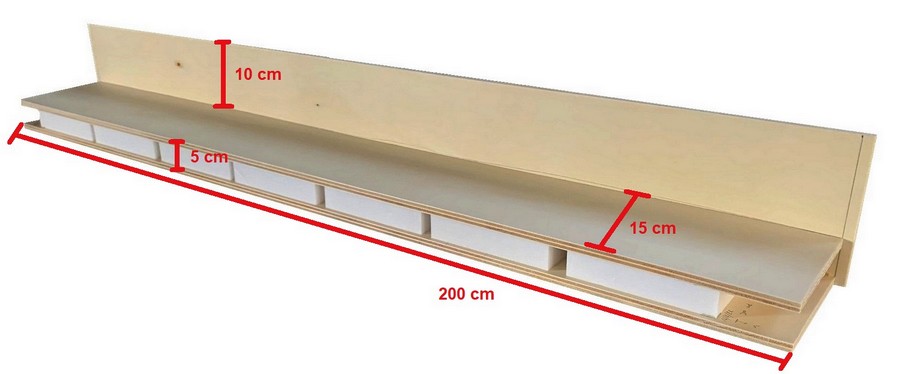 |
|
|
|
STRUCTURE #1:
THE WAREHOUSE
|
|
|
|
Even though the restricted size
of the layout clearly limited the possibilities
for structures, I wanted the two tracks and the
shuffling of rolling stock to convey a certain
meaningfulness. Having a modern-style warehouse
as a backdrop and a "destination"
wasn't very orginial, but since I already had the
Walthers "thin profile background
building" (something I would call
"low-relief") it was both an easy and
convenient choice to make. At 1-1/8 inches
(2.25 cm) the structure has a very shallow
footprint, yet its length of 19 inches (48.3 cm)
and its heigth of 4 inches (10 cm) result in a
fairly sizeable building, making it all the more
ideal for Pecan Street.
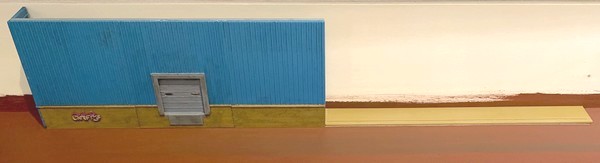
|
|
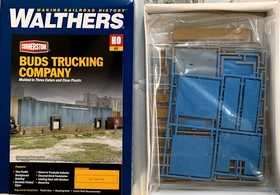
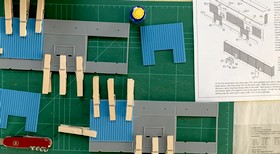
|
|
|
Since clearances are all important (and especially so
if you only have 6 inches to work with), assembling the
warehouse was the first step needed to provide a point of
reference for where exactly the tracks could go. At the
same time, the baseboard sides were added, and then a
liberal coat of acrylic paint sealed the baseboard top -
track ballasting and scenicking involves no small amount
of a mix of water and glue to fix it all in place, and
baseboards that haven't been sealed this way may well
start to warp. |
|
The low-relief warehouse kit is a
very straightforward build, as was adding two
Walthers SceneMaster modern-style wall lamps
along with some initial weathering using Vallejo
grey and black wash.
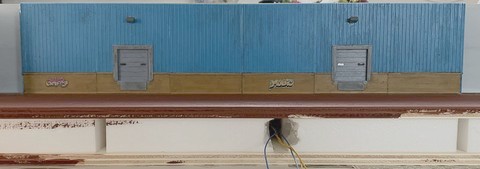
Having a narrow gap
between rolling stock and the warehouse front not
only results in a more prototypical appearance,
it also provides more room to space out the two
tracks a bit, making operation easier.
It is important to be
very diligent in this step, using the widest and
tallest item of rolling stock along with all
locomotives intended for use on the layout, to
ensure none of them fouls the warehouse.
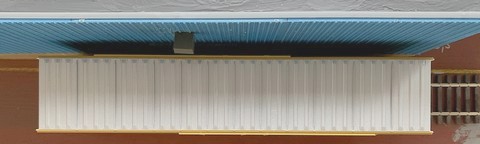
|
|
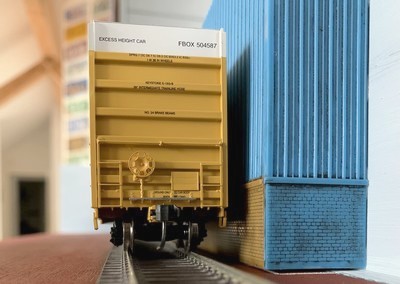
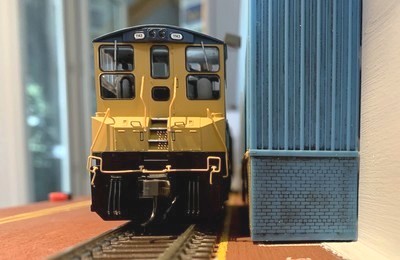 |
|
|
|
|
|
|
|
With all the clearances worked
out and marked down, it was time to lay the track
- once I decided which track to use. Peco is my
track of choice (due to decades of trouble-free
running) but that still left me with two options
for an HO scale layout: regular code 100 or code
83 US style track.
While the code 100 track has a slightly
chunkier rail profile, the most noticeable
difference is the smaller size and closer spacing
of the ties, giving the code 83 version a
distinctly more authentic "American"
look.
So why even hesitate?
|
|
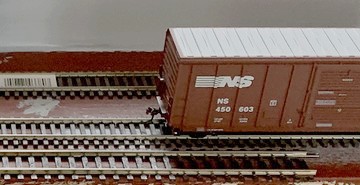 |
|
|
The sturdiness of Peco code 100
track is simply unsurpassed, and since Pecan Street would
require joining two segments every time it would be set
up (and then disconnecting those segments again for
storage), this seemed to be an aspect worth taking into
consideration. |
|
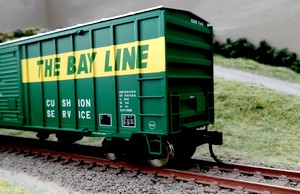 |
|
Not that
Peco code 83 is overly delicate, but the finer
rail profile does make it feel somewhat less
bombproof in comparison. As an added bonus, using
code 100 track would allow me to fall back on a
short piece of Peco setrack - the ultimate means
of connecting the two segments in a sturdy and
reliable way. Code 100 track would also allow me
to run some older models with oversize wheel
flanges. As for
the visuals, I had looked into that a few years
prior (for a US layout that ultimately never
materialized) by setting down a 50' boxcar on the
code 100 track of my Little Bazeley Mk1 layout.
Not surprisingly, with no code 83 track right
next to it for direct comparison, the weathered
and ballasted code 100 track didn't look too bad,
in spite of the "wrong" size and
spacing of the ties.
|
|
|
Ultimately, my decision was helped by looking at
prototype railroad locations around warehouses - and
seeing a clear and distinct potential for hiding any
perceived visual shortcomings of code 100 rail, since the
tracks in those places often convey an entirely different
look than what can be seen on a through traffic line. |
|
Looking north from a road
crossing on Titan Row in Orlando FL in 2021, we
see two modern warehouse structures served by two
sidings, along with a line that runs on to serve
more customers. The track here is far from
being dilapidated, in fact the through track
seems to have been re-ballasted recently and ties
replaced. But ballast on industrial trackage
often doesn't get tamped and regulated the way it
would on busier stretches of railroad track.
As a result, ties often get covered by ballast
both to the sides of the rails as well as in
their center, and over time, grass and weeds will
grow up in places.
A dry run using a piece of Peco code 100 track
showed that emulating this appearance on Pecan
Street would minimize the visual impression of
the larger and more spaced out ties.
As a result, I opted for sturdiness and proven
trouble-free running qualities and chose Peco
code 100 track for the layout.

|
|
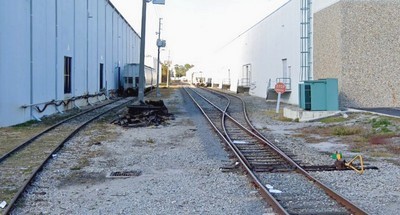
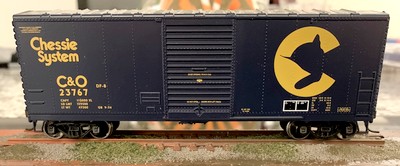
|
|
|
|
|
|
|
|
The simple track
configuration involved in a "tuning fork"
layout was thus laid using Peco code 100 track; Streamline
flextrack for the siding in front of the warehouse (since
this curves away from the single switch on this segment),
and pieces of Setrack "snap track" for
the siding running along the front of the layout (simply
because I had quite a stash of this available, and it
does make putting down a segment of straight trackage a
breeze). |
|
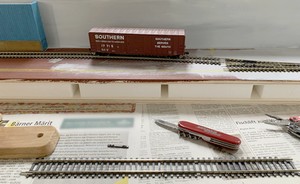
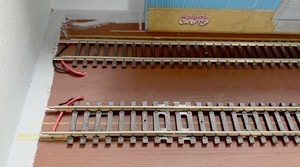 |
|
The switch is a Peco Streamline
medium radius "Insulfrog" point,
meaning it has an electrically insulated frog and
- unlike "Electrofrog" switches (that
have an electrically live frog) - requires no
extra wiring to operate, being DCC-friendly
straight out of the packaging.
The only snag
that "Insulfrog" points can throw up
with DCC operation is a potential shorting
problem with some metal wheels as they travel
through the frog. Even though this only seems to
be the case with a very limited number of
wheelsets, I decided to play it safe and add
insulator joiners to the inner rails past the
frog (as per the instructions printed on the Peco
packaging of the switch).
The illustration below is taken from my Little
Bazeley layout, but the principle remains the
same for any layout.
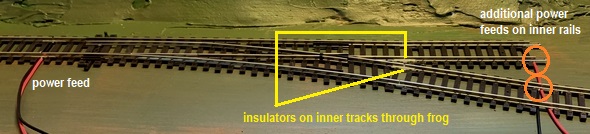
|
|
|
Once everything panned
out, the simple track configuration was laid down in
virtually no time at all. I like to make sure that the track is firmly and
securely attached to the baseboard (no roadbed needed for
industrial tracks) before weathering and ballasting,
which is why I use Marklin Z Scale track pins. Due to
their very small size these are very inconspicuous yet
still hold the track down perfectly well.
A test run then makes
sure that all electrical connections work properly.
|
|

|
|
There is also really
no difference in this case between an old-fashioned DC
wiring approach and a DCC friendly one. The only
difference are the additional feeder tracks
required due to the aforementioned insulator rail joiners
on the inner rails past the frog of the switch; I went
ahead and added additional feeders to both tracks at the
end of the two sidings to give this layout segment an
added boost in terms of feeding power to the track.
All
the wiring follows the common colour coding of
"black is at the back" (and therefore red wires
to the front rails).
|
|
|
|
|
|
|
As a first step in
weathering the tracks, I took the baseboard outside and
sprayed them a dark matt brown colour using an aerosol
spray can from the DIY store, masking parts of the switch
in order to avoid conductivity problems. |
|
 |
|
Like most modellers, I
have accumulated lots of "spare" items over the
years, and I felt that Pecan Street would be an excellent
opportunity to use items from this stash. |
|
However,
the rattle can that I still had left over from my
Little Bazeley Mk2 layout build a few months
back, proved to be a bad choice.
The spray paint went on
as usual and without any problems, but when I
tried to wipe the top of the rails immediately
after, I found that the paint was too sticky to
come off neatly - or even refused to do so at
all.
I suspect that
the aerosol/paint/solvent mix had deteriorated
inside the half-empty rattle can, but whatever
the exact reason, I had to apply a different
approach than I usually would. Deciding to let
the paint dry completely, I left it alone for a
good 48 hours. After this, I used swabs saturated
with isopropyl alcohol to wipe the top of the
rails clean.
|
|
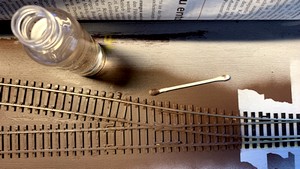 |
|
|
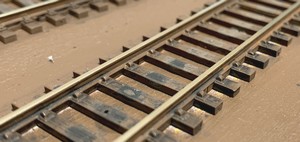
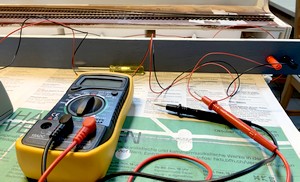
|
|
This
worked well (and without the damage abrasive
tools inflict on the rail surfaces), although the
paint was a bit more stubborn in some places,
requiring two or even three swipes. In the end, however,
this unexpected problem was solved and all the
rails had a shiny surface (necessary to provide
good electrical pickup). The masked-off section
at the switch was then touched up with a fine
brush and rust-coloured acrylic paint.
In order to
brake up the unrealistic uniformity of the
colour, I then added a few touches of RailMatch's
"sleeper grime" (an acrylic paint) as
well as some Vallejo grey and black washes
to the sleepers.
Even though
this is a very straightforward and simple way to
achieve a more realistic look, some (if not most
of it) would ultimately be lost - since I was
planning to "sink" the track and ties
well into the ballast. However, weathering the
track really is an essential part of recreating
the atmosphere of the real railroads, so I just
went ahead with it regardless.
More test
running and checking of all electrical
connections after this stage is essential to
discovering (and if needed ironing out) any bugs.
Once the functional aspects of the track are all
settled, it's time to add ballast to the
weathered track.
|
|
|
|
|
|
|
|
Having ballasted model
track for a good thirty years in HO/OO, N and Z scale, I
felt confident that my array of proven methods
accumulated over that period of time would provide me
with a trouble-free part of putting together Pecan Street
- especially since for the first time I would not be
attempting to produce a well-maintained and neat looking
section of ballasted tracks. I was in for something of a
surprise - and an extended episode of accidental
modelling. Initially though, everything went according to
plan.
|
|
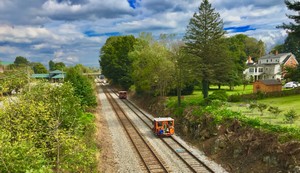
Track
maintenance work at Abingdon Va, 15
October 2018 (Video)
|
|
The colour of ballast varies
greatly on the prototype, depending on
the type of stone used and how much soil
and rust is deposited on the trackbed by
traffic on the line. A little bit of
research into the area and era modelled
(on location if possible, otherwise
online and through books and other media)
really helps to get it right. Unless you are
basing your layout on a specific location
with its own unique characteristics,
railroad sidings serving warehouses in
the US commonly seem to use grey, light
grey or buff coloured ballast.
I have
been using Woodland Scenics ballast
(actually made from crushed walnut
shells) for decades and saw no reason to
change that.
|
|
|
|
For this layout, I
opted for my favourite, the "fine" grade light
grey ballast (B74), which is usually marketed for N scale
and looks really good on HO track. With Pecan
Street, however, one
fundamental aspect of ballasting was different. |
|
Usually
(i.e. on all my previous layouts) I would try to
achieve a fairly neat appearance where the
ballast was evenly spread, with no loose
particles on top of the ties or clinging to the
rails. I would achieve this by sprinkling on only
small quantities from a teaspoon and then
straightening the ballast out using my index
finger, a fine paint brush, and a toothpick.
The basic idea is that
you can always go back for seconds and don't want
to use too much at once in order to avoid a mess.
It's also at this point that your Peco code 100
track (dismissed as "toylike" by some
modellers) really starts to shine.
|
|
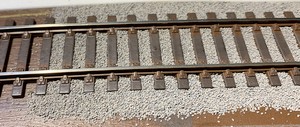 |
|
|
This time, though,
that "mess" which I would always try to avoid
was exactly what I now wanted for Pecan Street. |
|
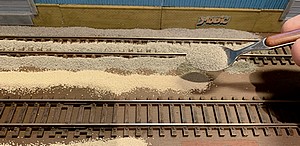
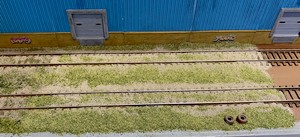
|
|
What
I didn't bank on was that I would find myself in
a little bit of a mess of a different kind. In spite of not having
to worry about not getting ballast everywhere, I
still tried to apply some amount of restraint.
Once I was
happy with the general look, I proceeded to
permanently glue the ballast down.
For decades I
have done this using what most modellers use: a
mix of water and white glue (approximately at a
1:1 ratio) with a drop of washing up liquid (to
break surface tension).
|
|
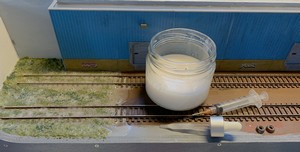
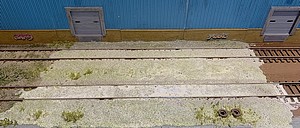
|
|
|
The mix is then carefully applied from a dropper,
which proved a better choice here than a syringe (both came from the vet). The
idea is to really soak the ballast, as this ensures that
the water/glue mix doesn't just cover the surface. Mixing white glue and water in this way
is a time-tested method for ballasting track, and once
applied it's best to leave everything to dry thoroughly
for at least 24 hours. |
|
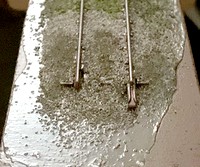 |
|
And this is
when things started to behave quite unlike what I
was expecting from my past experience. To kick things off, I found that
the white glue I was using dried perfectly clear,
but with a distinct and very glossy shine. While
this would be great if you modelled a scene
during or after a rainfall, it was not what I
wanted.
Maybe it was just that
make of white glue. Common modeller's wisdom has
it that the cheapest white glue you can get is
the best for this, but after testing out an
additional two or three brands I found that none
of them really dried with a matte appearance.
|
|
|
I noticed that all the
labels only specified that the glue would dry clear but
made no reference to a glossy or matte appearance. |
|
On top of this, I then noted a
second, completely unexpected problem with the
stretch of track that I had already ballasted. Even though I didn't
just throw down the ballast with wild abandon, I
found that after I had soaked the mix of Woodland
Scenics ballast and scenic scatter material
(still using the "trusted" mix of white
glue, water and a drop of dishwasher detergent),
it had a light but still distinct tendency of
expanding compared to what it looked like in its
dry condition.
The result was
a bit more "ballast and weed cover"
than I had aimed for. While the visuals were
fine, I found that running a "test car"
(in the form of a Walthers boxcar) over the newly
ballasted track did reveal two or three spots
where the ballast interfered with the wheel
flanges.
It wasn't that big a deal and easily rectified
by scraping away the few grains of ballast
causing the problem. Any small screwdriver or
similar tool will do the job.
|
|
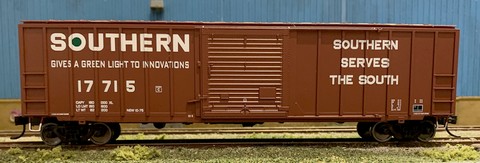
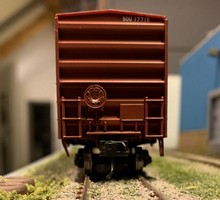
|
|
|
 |
|
In this case, however, I used a
cheap calculus scaler (I got mine on eBay) that
makes access easy and allows for a pin-pointed
removal of stray ballast. |
|
|
I was starting to realize that, contrary to
my initial assumption, covering ties in ballast
was actually more challenging than creating a
clean and neat spread of ballast around the rails
and ties. |
|
|
So
I made a point from this moment on of putting
down less ballast than originally intended,
especially between the rails.
This would make sure
there would be no problems with wheel flanges,
and potentially "underdone" spots could
always be touched up later.
|
|
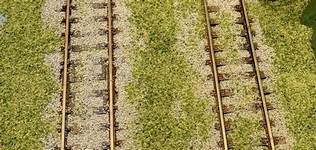
|
|
|
This did not, however,
fix the "white glue glossy finish" problem. Was
it possible that the formula for white glue had changed
across the board? Whatever the reason, I quite
unexpectedly found myself having to look for an
alternative solution. There were several options, but I
wanted something that wouldn't be too far removed from
what I had been using previously. And so I found myself
purchasing a container of Woodland Scenics Scenic
Cement™. |
|
 |
|
It solved my problem instantly, drying to a clear
matte finish and not "pushing up" the ballast.
For whatever reason (and it can't be too sophisticated),
this scenic cement worked while my trusted home-made mix
didn't. Of course there can't be too much of a difference
in terms of components (the scenic cement incorporates a
whetting agent, too) but since it worked and I wasn't
going to be needing gallons of it, that was all fine by
me. Sometimes there's nothing else to do but embrace
accidental modelling when it happens. From here on out, I
will be using Scenic Cement. Something I never do,
though, inspite of many positive reports from other
modellers, is "mist" the ballast with isopropyl
alcohol (IPA) before applying the water/glue mix. Even
when using a perfume atomizer, I have found that no
matter the distance from which the IPA is sprayed on it
tends to disturb the dry ballast - which is the exact
opposite of what this procedure is supposed to achieve.
|
|
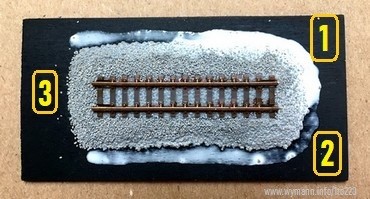 |
|
So instead of any
"pre-treatment", I simply apply the
scenic cement (or, previously, water/glue mix) by
taking advantage of its capillary force.
Because the scenic glue has a lower surface
tension than the ballast and scenic material
(thanks to the "wetting" agent),
applying the mix close to the edge of the ballast
(area #1 in the picture) results in the watered
down glue being drawn in and seeping into the dry
ballast by itself - or rather by its capillary
force (2).
Ultimately the effect is similar to blotting
paper or household tissues sucking up liquids,
and it leaves the ballast almost completely
undisturbed (3). The illustration used here shows
a piece of Z scale track, but the principle
obviously applies regardless of scale.
|
|
|
Letting the capillary force do its magic does however
result in a slightly slower procedure. Starting at the
edges of the area to be treated, patience is required to
then let the scenic cement work its way properly into the
ballast and scenic material (which might take a minute or
two). Additional scenic cement is then only applied to
the areas which have already soaked up the mix,
saturating them to the point where the mix then seeps
into the adjoining area of dry ballast and scatter
material. It is definitely a patience game, but then
ballasting shouldn't be rushed anyway. |
|
|
|
|
|
|
Since ballasting is best done in stages over several
days, I felt this was a good point in time to assemble
the second baseboard in-between ballasting sessions. It's
an almost identical twin, constructed using the same
methods a baseboard #1, except that I opted for one less
piece of styrofoam. Having six of those instead of seven
would give me more wiggle-room to run the wiring. |
|
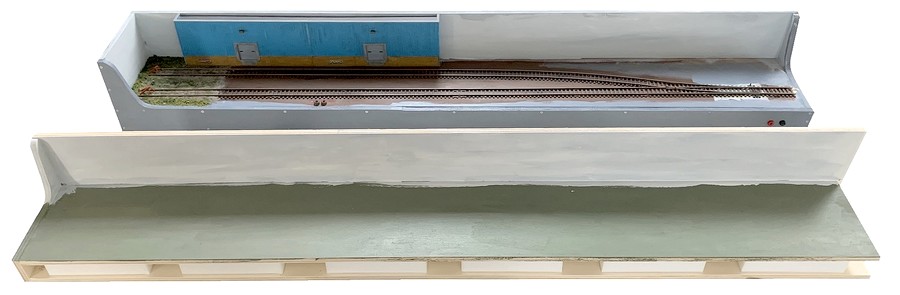 |
|
|
|
|
|
|
Pecan Street obviously doesn't allow for a lot of
scenery, but what little could be done on segment #1
would be situated towards the backscene and fulfill two
purposes: convey an atmosphere of a more rural than urban
setting, and hide the fact that the warehouse is nothing
more than a flat frontage essentially just stuck right
onto the backdrop. Taken together, those two points
would ideally result in a number of trees, but the layout
simply doesn't allow for that, so it would essentially
have to be shrubbery and possibly something akin to
low-relief trees. It is this kind of challenge that fuels
my appreciation of theatrical
layout design, since art directors in the
entertainment business often have to work with similarly
restricted spaces, be it on a theatrical or a movie
production stage.
|
|
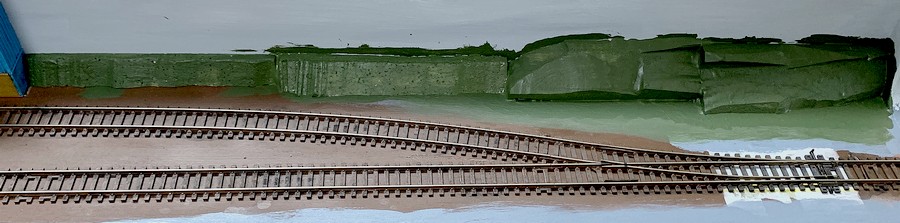 |
|
Since the shrubbery will be "growing" up
from the baseboard top to the backdrop, providing a base
which provides an additional vertical structural support
will make it easier to bring the shrubbery up higher so
the required effect will actually work. This base is
made up from four pieces of narrow styrofoam. They are
shaped to provide a slope and then covered in a very
thick layer of green acrylic paint - normally I would
cover the styrofoam with a layer of plaster of Paris but
this seemed like overkill in this situation. When all
will be done, nothing of that slope should remain
visible. The next steps on this will, however, only be
tackled once all the ballasting in that area is done.
|
|
|
|
|
|
|
Following the "heavy ballasting" around the
sidings, the area around the switch was ballasted with a
decisively lighter touch (and therefore more in line with
what I was used to from previous layouts). The idea here
is that the track is in the process of being somewhat
rehabilitated, as the tamped ballast along with a small
pile of fresh ballast besides the switch is supposed to
indicate. At a later point, the two slabs in the
background will support a few lengths of switched-out
worn and rusty rails. |
|
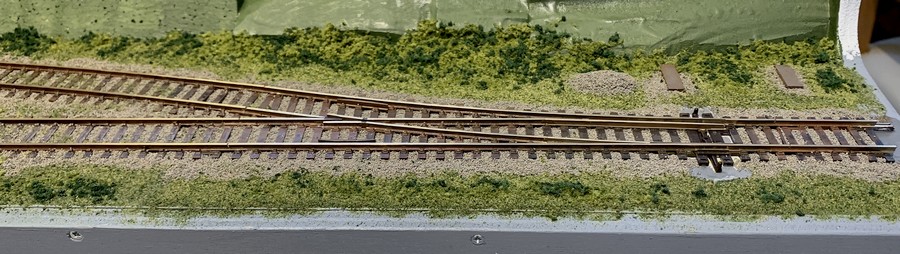 |
|
|
|
|
|
|
The narrow strip at
the back of the left-hand section of Pecan Street doesn't
allow for much in terms of scenery. The up side of this
is that a lot less scenic material is needed compared to
what would usually be the case. The possible down side:
the scenery needs to be carefully compressed in order to
look convincing. |
|
I
have always built up my layout scenery in layers.
This allows for a gradual build-up and blending,
which avoids an overly uniform look and also
makes tweaking things a lot easier. The first stage in
building up the background scenery to the side of
the warehouse was to cover the styrofoam base
with white glue; this serves as a base for a
generously applied mix of Woodland Scenics
"fine turf", mixing "green
grass" (T45, light to medium green) and
"weeds" (T46, medium to dark green).
This produces a
slope covered in low grass of various shades of
colour. It provides a pleasing enough look, but
more vegetation is clearly needed. Adding
different colour shades of Woodland Scenics
"bushes" (FC146 medium green, FC147
dark green, and FC149 forest blend) results in
another layer, and a more interestingly varied
backdrop scenery.
|
|
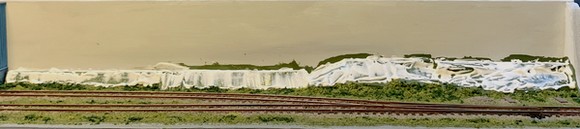
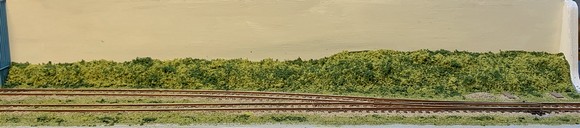
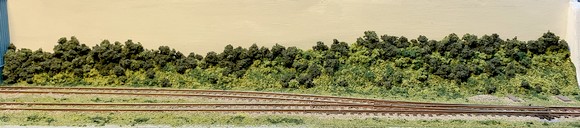
|
|
|
Having more dark colours towards the very back helps
to accentuate the perception of visual depth. For the
most part, this second layer is sufficient, since the
background scenery is supposed to be just that: its role
is not to attract attention but rather quite the opposite
- to just blend in with the backdrop (which, being of a
deliberately toned down "not so sunny sky"
tone, also doesn't detract from what is going on in the
foreground). |
|
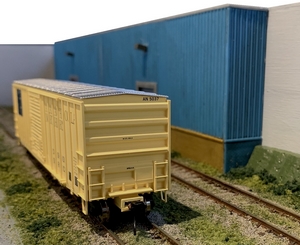 |
|
Using
low-relief buildings imitates a stage trick and
is a prime example of theatrical
layout design. But in order for this
visual deception to work, it is important to
disguise the true dimensions of such "stage
props" - the unhindered view of the shallow
sidewalls of the warehouse meeting up with the
backdrop is a dead giveaway at first sight.
The deception works as soon as that view is
obstructed, preventing a clear visual perception
of where exactly the warehouse ends and the
backdrop begins.
This is what stage designers do both in
theatres and on film production sets, and in this
case the effect is easily accomplished by adding
some sprawling vegetation in the form of trees
and tall bushes.
|
|
|
|
|
This sprawling vegetation is essentially a first
layer; refinements can be made anytime at a later stage.
It is formed of Woodland Scenics "bushes" (again mixing FC146 medium
green, FC147 dark green, and FC149 forest blend)
and "foliage" made up of various colours (F51
light green, F52 medium green, and F53 dark green). |
|
|
|
|
|
|
With the left hand segment of the layout having come
along quite a bit, work started shifting to the right
hand segment - and with it the question of how the two
segments would ultimately be joined up for operating
sessions. Although actually, that question had been
answered long before, since the possibilities of joining
up the two segments with a piece of setrack was an
important point in going for Peco code 100 track. |
|
Previous experience with modules has lead me to trade
visuals for truly secure physical and electrical track
connections across segments, and nothing beats having a
short piece of track as a "bridging" element. |
|
 |
|
The two segments of Pecan Street are joined up by a
very short (41mm) piece of track from the Peco setrack
range - a sturdy and reliable connection. The tracks on
both segments have been set back accordingly in order to
allow for a snug fit. Once both segments are fully
scenicked, the "connector track" can be
weathered in order to tone down the visuals. |
|
|
|
STRUCTURE #2:
THE COLD STORAGE
|
|
|
|
A true "tuning fork" layout only has a
single lead track running up to the point, but early on
in my planning I decided to add some additional visual
interest and operational potential by adding another
point on the lead track with a very short spur that would
hold one single piece of rolling stock only. In order
to give that single car spot some sense of being another
place that would have the odd boxcar or mechanical reefer
dropped off and picked up, I decided to go for the Dutch
company Artitec's low-relief kit of a cold storage
building that I had bought years ago (and is no longer
produced).
|
|
The kit is interesting in that it
is made from resin rather than plastic; this
allows for larger pieces with details moulded on.
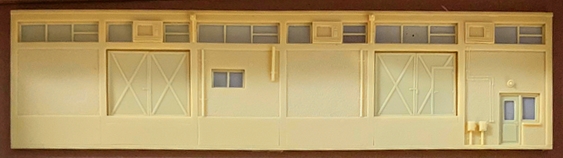
|
|
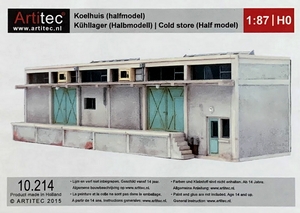 |
|
|
As a result, the entire model is made up of only a
handful of parts. Somewhat inspired by the rendition on
the box, I gave the few parts of the kit I would
ultimately be needing two coats of paint from a rattle
can - the first black (for contrast and texture), the
second a light spray of white. |
|
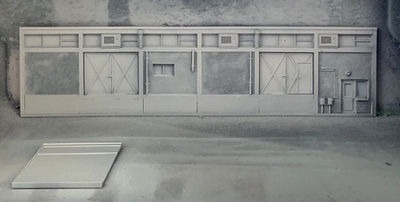 |
|
The
transformation from the original light yellow
colour is quite striking, and the rather finely
moulded details are nicely highlighted by the
darker shades from the first coat of spray paint. As straightforward as this model
is, it would need some adapting to fit the
reduced footprint available on the narrow layout.
First off, the already
low-relief model was reduced further in depth
from the original 5cm to just a tad over 2cm,
resulting in a setup almost identical to the
warehouse scene on the left hand segment.
To give the model a bit
more stability I cut a 2cm thick piece of
styrofoam to shape and glued it to the back of
the building's front
|
|
|
Since the roof moulding didn't
really work with the reduced depth of the model, I
replaced it with a simple piece of styrene and then added
the moulded loading platform and canopy as per the
instructions. |
|
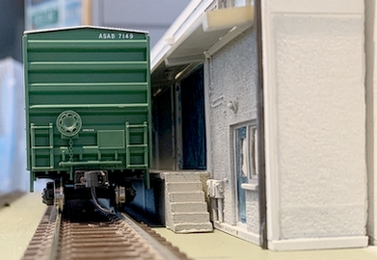
|
|
As
with the warehouse on the left hand segment,
getting the clearances right with this building
is the first step as these determine where
exactly the rails will go. And again the object was
to get cars fairly close up to the loading dock
edge, as this will eventually make things look a
lot more realistic.
Once the
measurements were all in, checked, and then
double and triple checked, laying the track was
next.
|
|
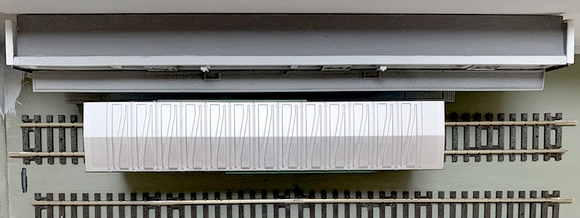
|
|
|
|
MORE TRACKLAYING
& WIRING
|
|
|
|
Following the same procedure for laying track and
wiring it all up as on the first, left hand side segment,
the simple track configuration (which is indeed identical
to the one on the left hand segment) was again made up of
Peco code 100 track Streamline
flextrack for the siding in front of the cold storage
building and pieces of Setrack "snap
track" for the siding running along the front of the
layout. |
|
 |
|
No changes to the switch arrangement
either, using
a Peco Streamline
medium radius "Insulfrog" point
and
adding insulator joiners to the inner rails past the frog
and extra wire feeds to all three segments of track, as
per Peco's instructions printed on the packaging of the
switch.
|
|
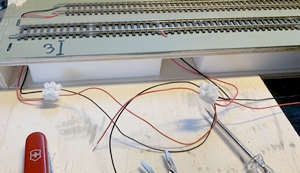 |
|
And again, Marklin Z Scale track
pins were used to attach the track firmly and
securely to the baseboard. Wiring such a simple
track configuration throws up no difference
between an old-fashioned DC wiring approach and a
DCC friendly one - although one could argue that
the way I brought together all three pairs of
feeder wires has a distinctly "old
school" look to it.
After the all important testing using a volt
meter to make sure that all connections work
properly and provide eletric current to all
segments of the track, weathering is next.
|
|
|
BACK
TO WEATHERING THE TRACK
|
|
|
|
|
|
Avoiding the mistake of using the
contents of an old rattle can, I spraypainted the
rails, masking off (again, as always) the part of
the point which is made up of moveable parts and
also ensures connectivity for the elctrical
current. Painting the rails outside on a hot
August afternoon in the midst of the 2022
heatwave made the paint dry really quickly, so
that it was impossible to wipe and clean all the
rail surfaces before the paint started to set.
But based on the experience with the left hand
segment, I knew not to worry and just let the
remaining paint dry properly. A day later I used swabs saturated
with isopropyl alcohol to wipe the top of the
rails clean.
In order to
brake up the unrealistic uniformity of the
colour, I also repeated the process of darkening
the ties, except this time I only used a
generous splash of Vallejo black wash (which,
when dry, is quite transparent).
Once all is set
for the moment, making sure all electrical
connections still work as they are supposed to is
certainly a good idea before moving on to the
next steps.
|
|
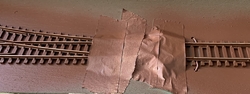
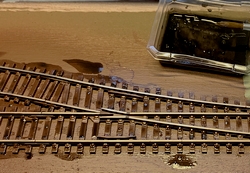 |
|
|
I did this following
my usual best practice (applying current from a standard
1980s DC controller and measuring the current in all
relevant places with a volt meter) but then also got out
my old Roco/Atlas GP40 from 1984 for some actual test
running - just a simple moment of inspirational nostalgia. |
|
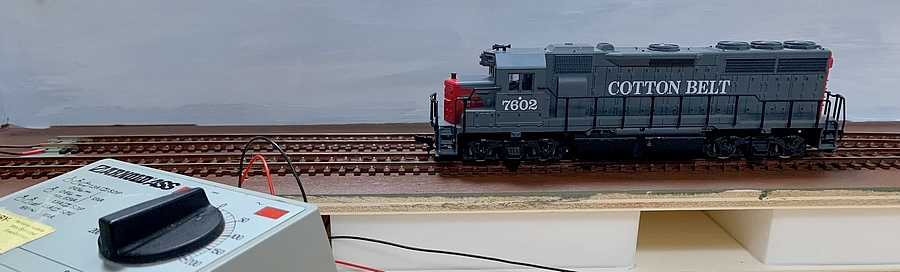 |
|
|
|
|
|
Prior to ballasting a few scenic items needed to be
put in place, and one of them was a grade crossing. Apart from providing an opportunity to
add some scenic interest, the crossing was intended right
from the start to mark a boundary for switching moves
when operating Pecan Street in "tuning fork
switching puzzle" mode. |
|
In essence, it
simply limits the length of a train (and
therefore the number of cars that can be switched
in one move) by having a rule in place which
states that the grade crossing cannot be blocked
during switching.
|
|
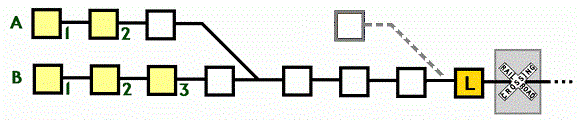 |
|
|
For this layout, I made a point of using as many
items as possible that I already had (i.e. purchased at
one time "for later"), and in my stash I found
a number of concrete grade crossing panels from BLMA
(since taken over by Atlas). |
|
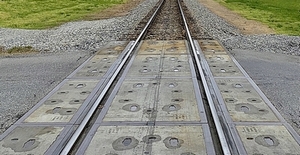
|
|
The nice thing about these was
that they not only fitted my very approximative
era very well (they have been used since the
1980s), but also happened to be the same type I
observed in April 2022, at a crossing over a
single Norfolk Southern track at Memorial
Hospital in Roanoke Va. The BLMA model consists
of two center panels and four side panels, but
given the restricted space I opted to use only
half of these components - which I would clearly
have to raise a bit since the packaging stated
that they would work from code 60 upwards.
|
|
|
The short stretch of road was built up around the
track using styrene sheets cut to shape, and the BLMA
panels brought closer to railhead level using styrene
shims. This is one of those occasions where a delicate
balance needs to be struck - setting the panel in between
the tracks too low will look terrible, setting it too
high will foul the couplers. As always with clearances,
it is best to use actual stock to make sure things fit;
in this case the central panel sits at a visually
realistic level - close, but not too close, for couplers
to clear it and run over it safely. |
|
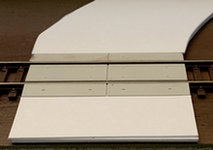
|
|
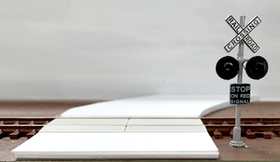 |
|
The crossing will be guarded by a
pair of signals with working lights, using a very
nice brass item bought on eBay. Holes to
accomodate the signals are drilled, and the road
is given a coat of medium-light grey; this will
serve as the basis for some overall as well as
detail weathering later on.
|
|
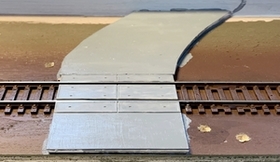 |
|
|
|
THE
END (A.K.A. CONNECTION TO
THE REST OF THE WORLD)
|
|
|
|
|
|
|
In essence, Pecan Street is a self-contained layout.
And whilst there are no plans to add any extension (such
as connecting it to more modules) for the foreseeable
future, adding the possibility to do so at this stage
makes sense. |
|
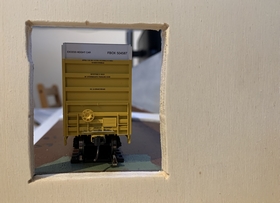 |
|
This also makes sense since there
is very little additional work involved in simply
cutting an opening into the sideframe (once again
making sure that the tallest and widest item of
rolling stock in use will pass through without
problems). On the layout itself, a scenic break
is needed to disguise the actual end of the track
regardless of whether it can be extended beyond
the baseboard frame or not.
|
|
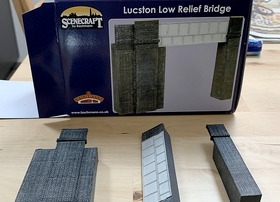 |
|
|
A chance discovery of a 2022 model of a low relief
bridge from the Bachmann (UK) range of
"Scenecraft" resin models provided just the
kind of "scenic disguise" I was looking for.
Although intended for British layouts, the design seemed
a good fit for a layout based on an East Coast location. |
|
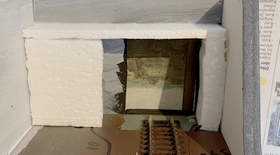 |
|
In order to work visually the
depth of this very low relief model had to be
increased quite a bit. This was achieved by
adding a structure made up of three pieces of
styrofoam cut to size. The result in itself is a
very crude contraption, but since the model
covers it up, this is all it takes.
|
|
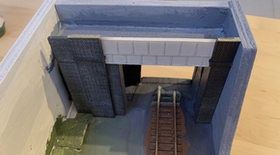 |
|
|
Black colour on the inside disguises the styrofoam
and creates enough of a "dark passageway" feel
to make it work as a scenic break - one of many
techniques I like to use that originally stem from theatrical
stage design. For the moment, that was it; the
obvious rough bits and edges would be patched up and
hidden in scenery after the adjacent scene of the track
crossing had been worked on. |
|
|
STAGE
TRICK: THE CROSSING
|
|
|
|
|
|
|
The narrow nature of Pecan Street poses a number of
challenges, some of which have already been mentioned.
Most of those boil down to the fact that there simply
isn't a lot of room for scenery - and the grade crossing
is certainly one of the areas on the layout where this is
felt the most. I have also mentioned how, in such
cases, I like to fall back on Frank Ellison's modelling
approach involving theatrical
stage design - and this is perhaps also most apparent
in how the grade crossing is set up on Pecan Street.
|
|
In its raw modelling state, the
road crossing the tracks curves away slightly in
order to provide at least some illusion that it
doesn't just hit the backdrop in a head-on
collision, but it still clearly ends right there,
a mere 3.5 inches (9 cm) away from the track. In
order to conceal this, a number of steps would be
necessary to create an illusion of depth, and one
central prop was a rather nice model of a truck,
manufactured by a company named Boley, that I had
bought cheaply and put aside years ago for
"some future project". Now, it would
literally take center stage.
|
|
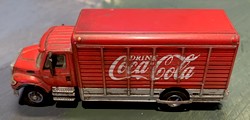 |
|
|
But before that could happen, the stage itself had to
be set. The idea was to add a flat photographic backscene
to the backdrop, and then add some semi-relief props to
make the scene look threedimensional and create the
impression that the road crossing the tracks actually
went somewhere in the background. After finding a
suitable royalty-free image on the web, this was reduced
to the required size, cut out and glued onto sturdy 2mm
cardboard, and given a protective layer of matt varnish.
This was then in turn glued to the backdrop, and a first
batch of scenic material applied to cover both the edge
of the card and fill in a gap between the overbridge and
the backdrop. For the more three-dimensional props, two
large scenic trees were cut in half and then glued into
place.
|
|
|
The trees
came from a range that can generally be
termed "cheap model trees from China
sold on eBay". They are somewhat
infamous for their overall identical
appearance (which of course explains the
cheap price) but also rather popular,
since it is fairly easy to improve their
looks. Usually the excuse for giving
these a go is the sheer number of trees
needed and the cost involved, but I still
happened to have these lying around after
a curiosity purchase and successfully (I
felt) "pimping" them with
Woodland Scenics foliage for use on Little
Bazeley.
|
|
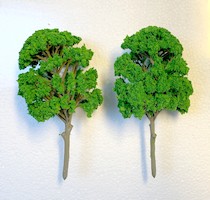 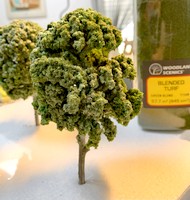 |
|
|
|
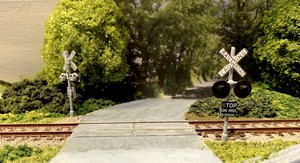
|
|
Building up more layers of
scenery (mixing Woodland Scenics fine and coarse
turf, foliage and bushes of various colour
shades) allows the foreground to blend with the
flat backscene, further enhanced by some
strategic "shadows". As on a theatrical
stage, it is all aimed at deceiving the onlooker
into believing that the scene has more depth and
reaches further back than it actually does. The
scene could be left this way, but in order to
fool even a lingering observer a bit longer, the
aforementioned truck is placed as a view block
which also deflects attention from the flat
backdrop to an actual three-dimensional prop in
the foreground.
|
|
|
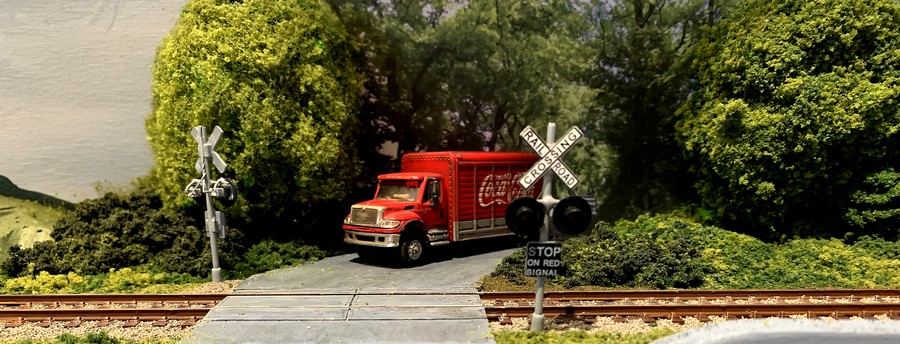 |
|
In order to achieve this illusion, some further
theatrical trickery is necessary - what seems to be a
truck is actually only part of one. Cutting down the
rear of the vehicule at a 45º angle not only allows a
longer vehicule to be squeezed into what little space
there is, it can then also be placed in a skewed position
(another theatrical trick for props that are supposed to
fool our sense of perspective).
|
|
|
Taking apart the truck for the
procedure was also a good opportunity to fit a
driver behind its wheel - a suitably cut-up
Preise figure from a set of track maintenance
workers. It's another stage setting adage: things
that are there may not always get noticed, but
things that are missing most certainly will. In
a perfect world, I would have turned the front
wheels somewhat, but simply thought of this too
late - so I simply imagine the driver is just
about to apply the steering wheel...
|
|
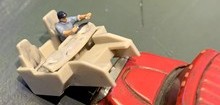 |
|
|
|
BACK
TO BALLASTING &
SCENERY
|
|
|
|
|
|
|
With the crossing scene set up, the rest of the
remaining portion of the second, right-hand segment, was
to be given a fairly straightforward treatment in terms
of ballasting and background scenery. |
|
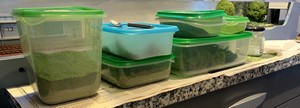
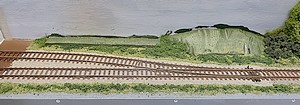
|
|
So out came my array of
transparent household storage boxes, holding the
contents of various bags of ballast and scenic
material (mostly from the Woodland Scenics
range). The usual pieces of styorofoam were
cut, glued down and given a heavy coat of dull
green acrylic paint in order to serve as contours
for the background scenicking in front of the
backdrop.
As for the ballasting I decided to generally
keep it fairly neat on this part of the layout
compared to the warehouse segment. The basic plan
was to see how things would look once completed
that way, and then add more ballast or weeds on
top of the already ballasted track if needed.
|
|
|
|
|
Once tamped down this
way, more ballast can be added where needed (which is a
lot easier than getting rid of too much ballast). It is
impossible to avoid getting at least a little bit of
ballast where it shouldn't be (e.g.on the sides of the
rail), but all it takes to remove this is a gentle
approach using a fine brush and a toothpick along with
some patience. |
|
Once
everything looks okay, scenic cement is applied
from a dropper to the edges of the ballasted
area, letting the ballast and scenic material
soak it up thanks to capillary action. Adding
more scenic cement to areas already soaked in it
will make it "spread" to areas that are
still dry. Again, some patience is required, but it
doesn't take too long and causes minimal
disturbance to the unsecured ballast grains (glue
applied directly to dry ballast will cause it to
float and drift around). Since taking advantage
of capillary action for ballasting, I have in
essence switched from using a syringe to a simple
drop dispenser with a rubber teat, since the
latter provides a more controlled and gentle
application.
|
|
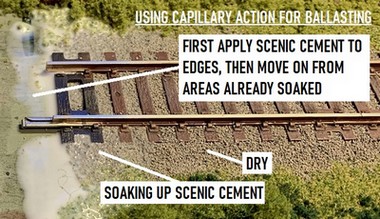 |
|
|
Again, the scenic ground cover is built up in steps by first covering the
painted styrofoam bases with white glue, which in turn is
covered with a mix of Woodland Scenics "fine turf
green grass" (T45, light to medium green) and
"weeds" (T46, medium to dark green) in order to
avoid a uniform look. Adding different colour shades of
Woodland Scenics "bushes" (FC146 medium green,
FC147 dark green, and FC149 forest blend) then results in
another layer, which is secured with scenic cement. |
|
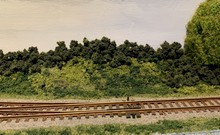 |
|
In order to provide a smooth
transition to the road crossing scene, a short
tree line needs to be built up along this basic
scenery - which means more tweaking and pruning
of some "cheap model trees from China sold
on eBay". |
|
|
Since this is strictly background scenery and
therefore explicitly not supposed to attract attention
away from the foreground, it's not about detail but
rather the overall impression. |
|
Tree stems
therefore do not need to be visible, even
more so since the trees are heavy and
dense in foliage (a real life example of
such a tree would be the Arborvitae
Tree). This in turn means that I really
cut into the "plastic skeleton"
of these trees, leaving only a minimal
number of unconnected
"branches" - they won't be
visible, but this provides just the right
amount of structural cohesion and
flexibility at the same time. The cut-up
structure of the tree still shows off
some of the very bright green the tree
originally comes in, but once it's all
turned around the Woodland Scenics
foliage hides practically all of that.
|
|
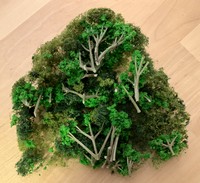 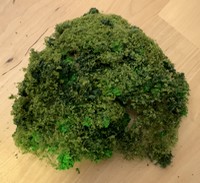 |
|
|
|
 |
|
Since the layout itself only has a very shallow depth
of 6 inches (15 cm), the background scenery needs to be
extremely compressed. It would be almost impossible to
fit an actual complete model of a tree into a space of 2
inches (along the single track), let alone into the
cramped quarters of just one inch (along the segment with
the mainline and the spur). Cutting up the trees is
therefore very much the equivalent of having
super-low-relief structures (as, indeed, the storage
building on the spur is). |
|
 |
|
This also means that the tree line needs to be dense;
too much light foliage which would allow the onlooker to
see through the trees would be a dead giveaway. Stage
designers have developed many different tools to creating
the illusion that a scene is much deeper than it actually
is, and this is just one example of how applying theatrical
stage design to a layout works. Another trick of the
trade applies to hiding the true dimensions of low-relief
buildings. As with the warehouse on the left-hand
segment, an unobstructed view of the storage building on
this segment will clearly show that the side walls are
very shallow since they meet up with the backdrop almost
immediately.
In order to create the illusion of an actual building
that reaches further into the background (as a real
structure would) the view of the side wall needs to be
obstructed, This is exactly what stage designers do both
in theatres and on film production sets, and in this case
the effect is easily accomplished by again adding some
sprawling vegetation. On the more visible right hand side
of the building the tree line meets up with it, along
with some shrubs and bushes. For the left hand side of
the building - which is in the far left corner of this
segment and thus less open visually - I opted for a more
refinde model of an individual tree.
|
|
|
|
Unlike the cheap quantity-over-quality plastic
examples from China, this one was hand-made in Vietnam
using strands of wire to simulate the bark and branches
more realistically (as is the foliage). Also available on
eBay, these trees are of a far superior quality, but
obviously also carry a higher price tag (you get what you
pay for). The corner seemed a good spot to
"plant" such a model - visible enough, but not
too much. The tree is used as is, with no cutting, and it
does protrude slightly out into the spur a bit, but since
its location is the end of the line for that siding, this
isn't a problem. |
|
Building up
the scenery in layers like this also has
the distinct advantage that it's always
possible to go back and add more shrubs,
bushes, weeds and other items later on. But
already at this point, the background
scenery fulfills its purpose. It provides
a setting, disguises the otherwise
obvious spatial limits of the layout, and
overall sets the mood of the scene. And
of course it works best when there's
something in the foreground that shifts
the focus of attention.
|
|
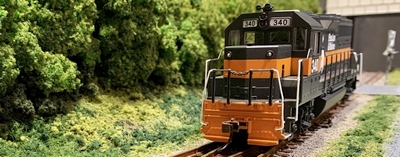 |
|
|
|
Work in progress, more
to come...
|
|
|
|
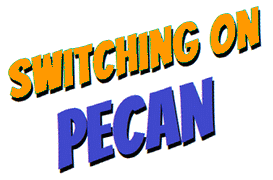
|
|
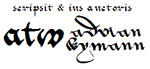
Text and
pictures are (c) 2022-2024 Adrian Wymann.
|
|
page created 12 March 2022
last updated 21 June 2024
|
|
|